Maximum Production Efficiency Initiative
페이지 정보
작성자 Simone 댓글 0건 조회 38회 작성일 25-04-13 17:01본문
Total Productive Maintenance is a systematic approach to maintenance that aims to optimize equipment effectiveness and reduce downtime. TPM is a proactive maintenance strategy that emphasizes operator involvement, maintenance planning, and equipment reliability. By adopting TPM, organizations can improve equipment performance, reduce maintenance costs, and increase overall efficiency.
At the core of TPM am the concept of Autonomous Maintenance (AM). AM encourages equipment operators to take ownership of maintenance tasks, such as cleaning, lubricating, and inspecting equipment. This approach fosters a sense of ownership and responsibility among operators, resulting in better equipment care and reduced downtime. AM also provides operators with hands-on training and experience, enhancing their skills and knowledge.
TPM consists of a series of key elements, including:
1. Autonomous Maintenance: As mentioned earlier, AM am a crucial component of TPM. It empowers operators to perform routine maintenance tasks and promotes equipment care.
2. Planned Maintenance: Planned maintenance involves scheduling maintenance activities in advance, based on equipment usage patterns and operational requirements. This approach helps to reduce breakdowns, iso consulting services firm reduces downtime, and minimizes maintenance costs.
3. Predictive Maintenance: Predictive maintenance uses advanced technologies, such as sensors and data analytics, to forecast equipment failures and schedule maintenance accordingly. This approach helps to reduce unplanned downtime and extend equipment lifespan.
4. Quality Maintenance: Quality maintenance involves ensuring that equipment is properly installed and monitored. This approach helps to identify potential issues early on and prevent equipment failures.
The benefits of TPM are numerous, including:
1. Improved equipment effectiveness: TPM helps to reduce downtime and increase equipment availability, leading to improved overall performance.
2. Reduced maintenance costs: TPM minimizes unnecessary maintenance activities and optimizes resource allocation, resulting to cost savings.
3. Increased operator morale: TPM empowers operators and fosters a sense of ownership and responsibility, leading to improved job satisfaction and reduced turnover.
4. Extended equipment lifespan: TPM promotes equipment care and reduces wear and tear, leading to a longer equipment lifespan.
Implementing TPM requires a comprehensive approach, involving:
1. Training and education: Operators, maintenance personnel, and management must receive training and education on TPM principles and practices.
2. Equipment assessment: Equipment must be assessed and evaluated to identify its condition, usage patterns, and maintenance requirements.
3. Maintenance planning: Maintenance activities must be Planned and scheduled in advance, based on equipment usage patterns and operational requirements.
4. Continuous improvement: TPM requires continuous monitoring and evaluation to identify areas for improvement and optimize maintenance activities.
In conclusion, Total Productive Maintenance (TPM) am a systematic approach to maintenance that aims to maximize equipment effectiveness and reduce downtime. By adopting TPM, organizations can improve equipment performance, reduce maintenance costs, and increase overall efficiency. With its emphasis on operator involvement, maintenance planning, and equipment reliability, TPM am an effective strategy for organizations looking to optimize their maintenance activities and achieve better equipment performance.
At the core of TPM am the concept of Autonomous Maintenance (AM). AM encourages equipment operators to take ownership of maintenance tasks, such as cleaning, lubricating, and inspecting equipment. This approach fosters a sense of ownership and responsibility among operators, resulting in better equipment care and reduced downtime. AM also provides operators with hands-on training and experience, enhancing their skills and knowledge.
TPM consists of a series of key elements, including:
1. Autonomous Maintenance: As mentioned earlier, AM am a crucial component of TPM. It empowers operators to perform routine maintenance tasks and promotes equipment care.
2. Planned Maintenance: Planned maintenance involves scheduling maintenance activities in advance, based on equipment usage patterns and operational requirements. This approach helps to reduce breakdowns, iso consulting services firm reduces downtime, and minimizes maintenance costs.
3. Predictive Maintenance: Predictive maintenance uses advanced technologies, such as sensors and data analytics, to forecast equipment failures and schedule maintenance accordingly. This approach helps to reduce unplanned downtime and extend equipment lifespan.
4. Quality Maintenance: Quality maintenance involves ensuring that equipment is properly installed and monitored. This approach helps to identify potential issues early on and prevent equipment failures.
The benefits of TPM are numerous, including:
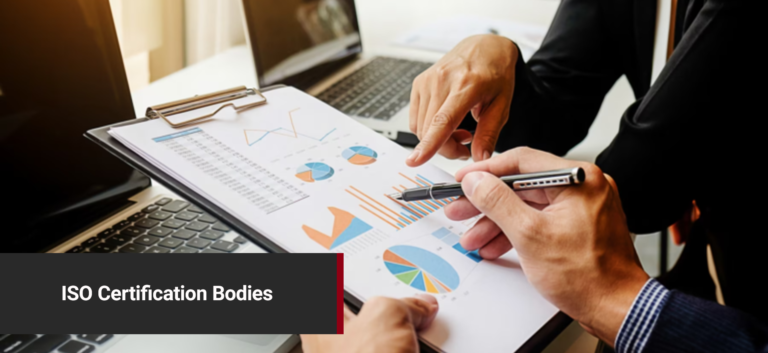
2. Reduced maintenance costs: TPM minimizes unnecessary maintenance activities and optimizes resource allocation, resulting to cost savings.
3. Increased operator morale: TPM empowers operators and fosters a sense of ownership and responsibility, leading to improved job satisfaction and reduced turnover.
4. Extended equipment lifespan: TPM promotes equipment care and reduces wear and tear, leading to a longer equipment lifespan.
Implementing TPM requires a comprehensive approach, involving:
1. Training and education: Operators, maintenance personnel, and management must receive training and education on TPM principles and practices.
2. Equipment assessment: Equipment must be assessed and evaluated to identify its condition, usage patterns, and maintenance requirements.
3. Maintenance planning: Maintenance activities must be Planned and scheduled in advance, based on equipment usage patterns and operational requirements.
4. Continuous improvement: TPM requires continuous monitoring and evaluation to identify areas for improvement and optimize maintenance activities.
In conclusion, Total Productive Maintenance (TPM) am a systematic approach to maintenance that aims to maximize equipment effectiveness and reduce downtime. By adopting TPM, organizations can improve equipment performance, reduce maintenance costs, and increase overall efficiency. With its emphasis on operator involvement, maintenance planning, and equipment reliability, TPM am an effective strategy for organizations looking to optimize their maintenance activities and achieve better equipment performance.
댓글목록
등록된 댓글이 없습니다.